What Are Engineering Guidelines for Additive Manufacturing? 2024 Guideline
- January 12, 2024
Commonly known as 3D printing, design for Additive Manufacturing (AM) has streamlined the way we design products. Unlike traditional manufacturing methods, AM builds objects layer by layer. You can get and overcome unique opportunities and challenges.
Engineering Guidelines for Additive Manufacturing are essential for you if you want to develop a career in this line. Let’s learn more about it.
What Is Additive Manufacturing?
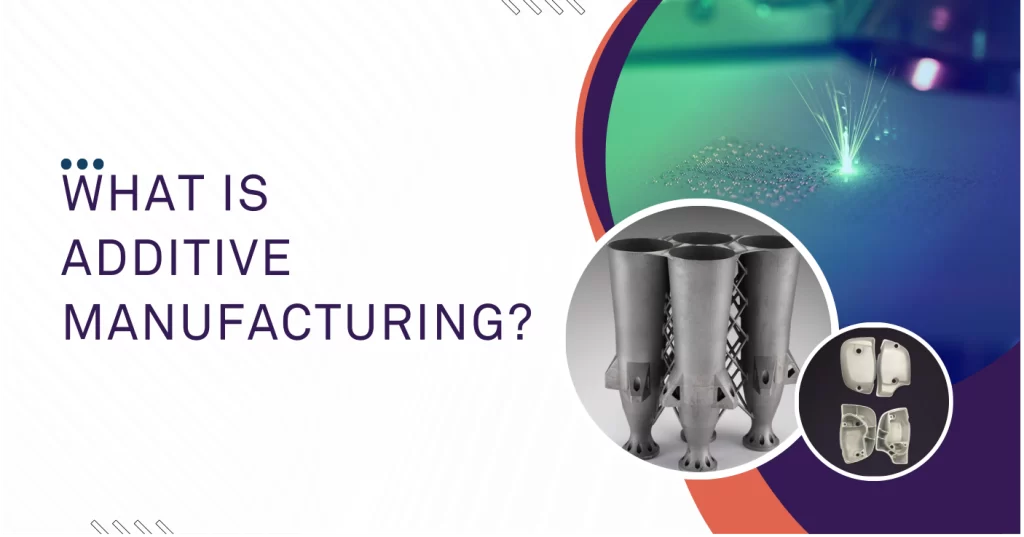
Often known as 3D printing, AM is a remarkable method for creating objects layer by layer. This technology uses different modern methods.
Unlike traditional manufacturing, which subtracts material to create a product, AM adds material incrementally. Imagine building an object by stacking individual slices – that’s essentially how AM works.
Consider it like a hot glue gun building up layers of melted plastic to create a 3D shape. It’s a layer-by-layer approach and offers incredible design flexibility and complexity.
You can easily produce intricate structures which are challenging or impossible with traditional methods.
AM comes in different flavors, such as Fused Deposition Modeling (FDM), Stereolithography (SLA), and Selective Laser Sintering (SLS). Every method uses specific materials like plastics, metals, or even ceramics.
It has widespread applications. Such as creating prototypes and custom medical implants to producing spare parts on demand.
AM is a groundbreaking method. It adds material layer by layer to form 3D objects. Also, you have new scopes for design. And manufacture across different industries.
What Are the Engineering Rules of Design for Additive Manufacturing?
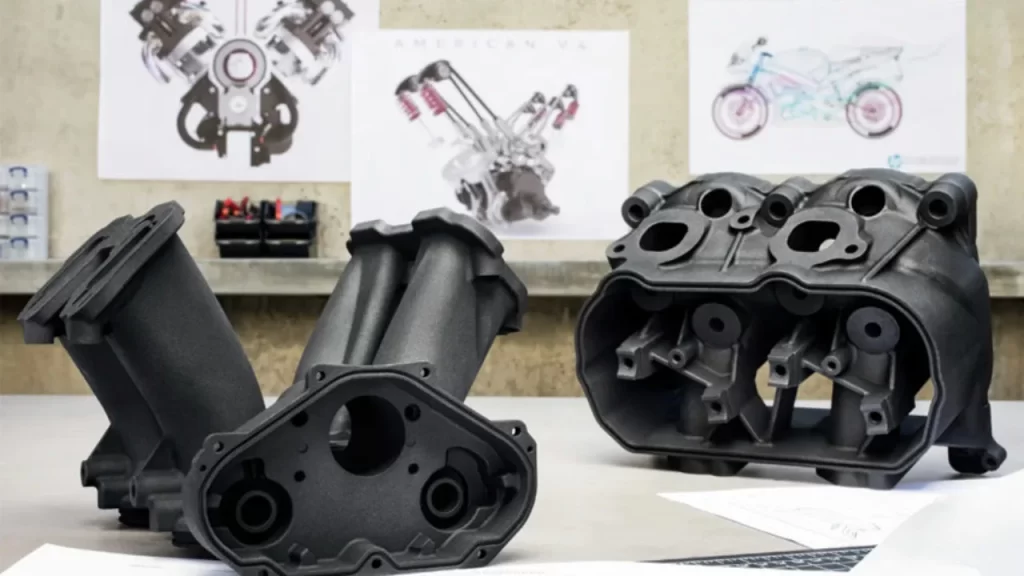
It’s important to know the engineering rules for additive manufacturing. It will help you earn solid ground before you set for the world. We have combined our list of 7 best engineering rules of design for additive manufacturing. Take a look below,
1) Design for Layer-by-Layer Construction:
In 3D printing, making things layer by layer is like building a delicious sandwich, placing one ingredient at a time. Designers should be like chefs, creating shapes that match this layer-by-layer style.
Avoid making parts that stick out too much, just like you wouldn’t want your sandwich ingredients falling off. Also, think of how the object should turn out during printing. It helps you deliver a strong and steady project.
2) Material Selection:
Picking the right material for 3D printing is like choosing the right tools for a job. Different 3D printers use different materials. It can be plastics, metals, or ceramics. It’s as if whether to use wood or metal for a project. Engineers need to think about what the thing they’re making needs – is it strong, flexible, or resistant to heat?
3) Support Structures and Overhangs:
If you were building a tower with blocks, you would need support so it doesn’t fall. In 3D printing, we want to avoid needing too much support. Overhangs, or parts that stick out too much, might need extra help. Designing things that can support themselves is like building a tower that doesn’t need a lot of extra blocks.
In 3D printing, overhangs (like the edges of a roof) can be a challenge. Designing structures that can stand on their own is like making a sandcastle with sturdy walls that don’t collapse.
4) Wall Thickness:
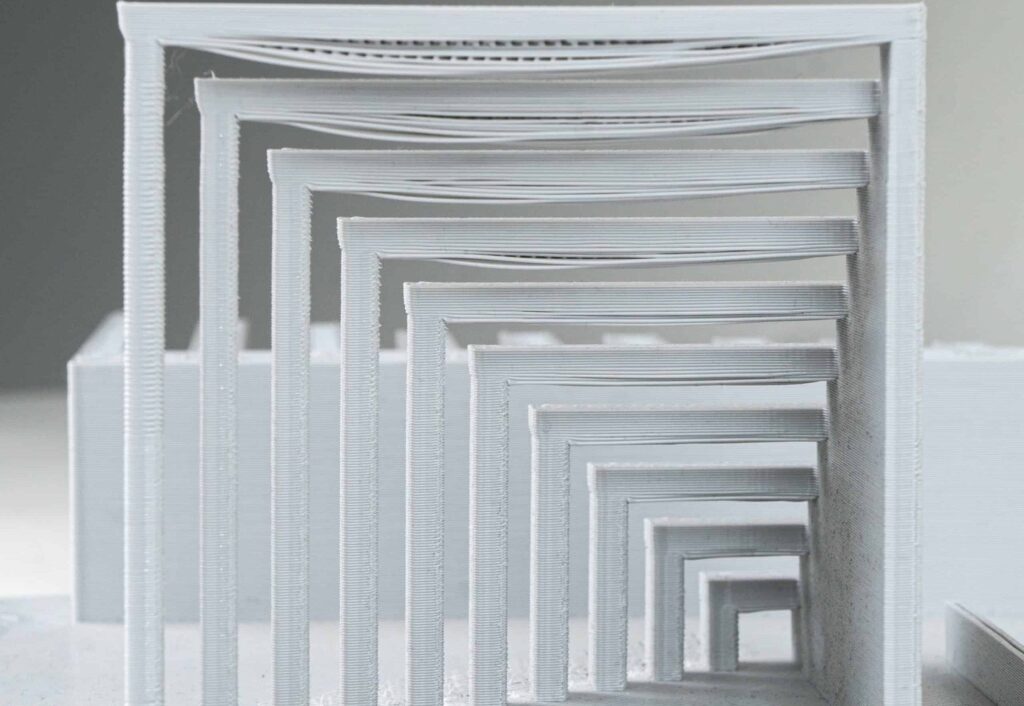
For our 3D printed object to be strong, we need to make sure its walls are not too thin, like paper, or too thick, like a brick wall. Finding the perfect balance is like making sure the walls of our tower are just right – not too thin to be weak, and not too thick to use too much material.
Just like the walls of a house, the thickness of 3D-printed parts is vital. Too thin, and it might be fragile like a paper cup; too thick, and it’s like using too much clay–heavy and slow to build. Striking the right balance ensures the printed object is strong and efficient.
5) Tolerance and Clearance:
In 3D printing, machines might not be perfect, so designers need to account for a bit of wiggle room. Imagine building with blocks – they need space to fit together nicely. Designers must leave enough room between moving parts so that they don’t get stuck, just like ensuring the blocks don’t get jammed.
6) File Format and Resolution:
For 3D printing to work, designs need to speak the right language, like using the correct recipe. STL is the language that 3D printers understand. Think of it like sending a letter – use the right envelope (file format) and make sure the writing (resolution) is clear. Higher resolution is like sharper writing, but it might take longer to send.
7) Iterative Prototyping:
3D printing allows for trying things out before making the final version. It’s like baking cookies – you taste a small batch first. Use the quick and flexible nature of 3D printing to make prototypes, testing and adjusting your design until it’s just right, like perfecting your cookie recipe before baking a big batch.
Why Engineering Guidelines for Additive Manufacturing Is Important?

Engineering guidelines for Additive Manufacturing (AM) are important for several reasons. It develops a structured approach to design and production. Take a look below,
1) Optimized Performance:
AM offers unique design possibilities, and guidelines help engineers leverage these capabilities effectively. Engineering guidelines ensure optimized designs for the layer-by-layer construction method. It also leads to improved structural integrity and overall performance.
2) Material Suitability:
Different AM technologies support various materials, each with distinct properties. Guidelines aid in selecting the most suitable material for the intended application. It considers factors like strength, flexibility, and heat resistance. Proper material selection ensures that the final product meets specific functional requirements.
3) Efficient Resource Utilization:
Designing with consideration for factors like wall thickness and support structures helps in minimizing material usage. This efficiency is not only cost-effective but also aligns with sustainability goals by reducing waste.
4) Less Print Failures:
Guidelines regarding overhangs, support structures, and wall thickness contribute to the prevention of print failures. Designs that are not aligned with AM principles may result in defects or require additional post-processing efforts.
5) Design Consistency:
Tolerance and clearance guidelines ensure that designs are compatible with the inherent variations in print accuracy. It delivers consistent and reliable results across multiple prints. The possibility of errors is also less.
As AM technology continues to advance, engineering guidelines for additive manufacturing help you stay ahead of developments.
You can stick to established principles. Now, with guarantee that your designs remain relevant and capitalize on emerging capabilities.
Moreover, guidelines help you reveal the full potential of transformative technology. Designers and engineers have a roadmap to guide them toward success. After all, optimized outcomes are always better for 3D printing.
Final Words:
Following these rules for 3D printing is like having a helpful map for a journey. Our guidelines help engineers make the most of Additive Manufacturing. We can assure you, that the designs are strong, the materials are just right, and things fit together well.
Stick to engineering guidelines for additive manufacturing. Together, we can avoid problems, save time and money, and make cool things with 3D printing.
It’s like having a recipe for success – following the steps ensures a tasty result. So, in the world of 3D printing, let’s keep following these guidelines to create amazing stuff, one layer at a time!